Self-Healing Concrete – A Potential Sustainable Solution for Durable Concrete Structures
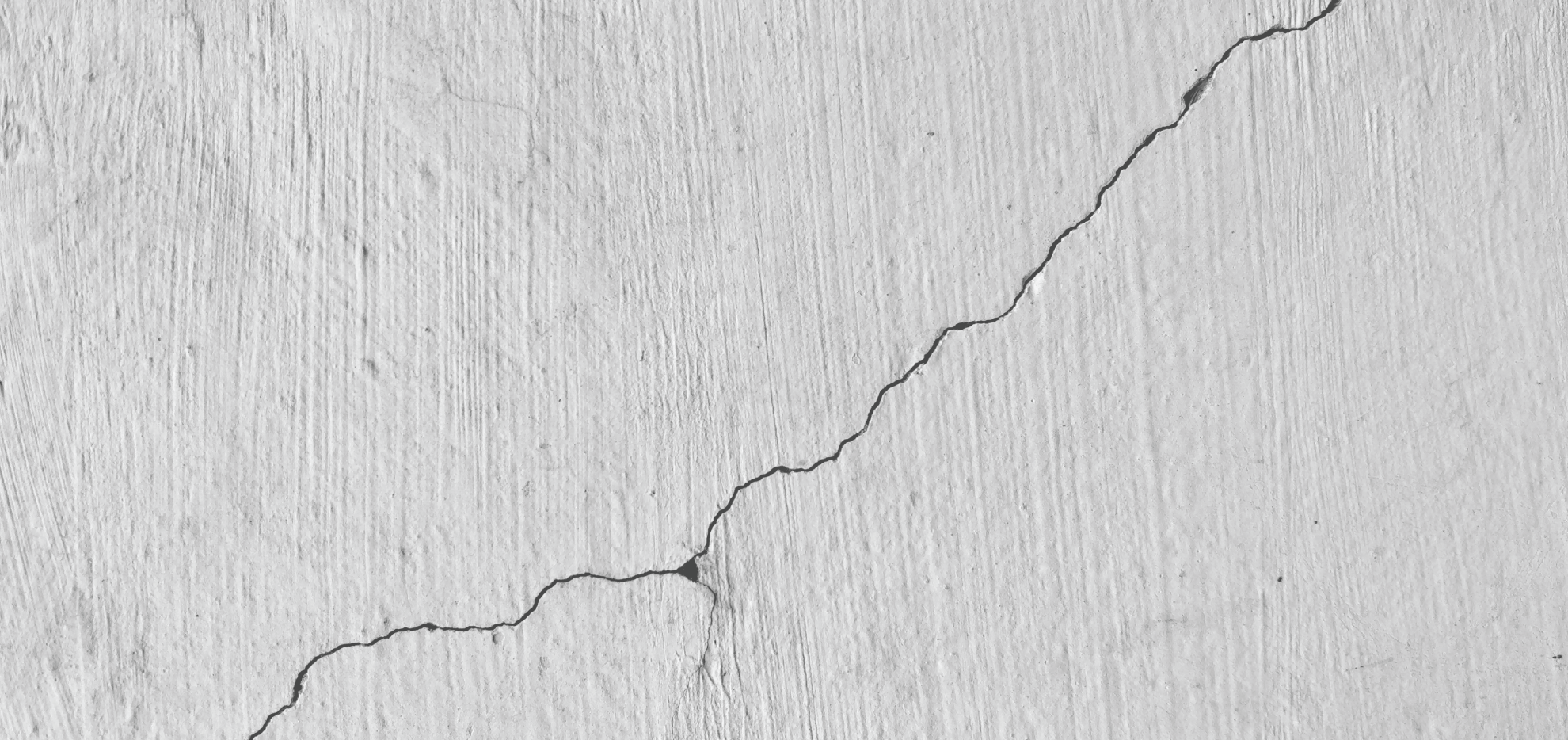
Concrete is a popular construction material due to its large-scale usage in infrastructure and industrial structures. In modern construction technology, continuous efforts are being made to enhance the durability of concrete with reduced maintenance. Self-healing concretes may be considered a sustainable solution for achieving almost crack-free concrete in the life cycle of a structure. Various self-healing technologies can be adopted depending on different applications, some of which are discussed here. While self-healing can be autogenous with zero or very less initial expenditure but with very limited performance, more durable and maintenance-free solutions may be achieved with autonomous self-healing techniques at a cost of some initial investments. Though, invented way back in 2006, mass use of self-healing concrete, in reality, is still a challenge due to inadequate validation concerning reactivity with admixtures, cost, long-term sustenance etc. The effect of various kinds of exposure conditions on the self-healing performance of concrete is also briefly narrated to explore further possibilities of adopting such technology in real-life applications.
Introduction
Concrete has emerged as a popular construction material worldwide due to its durability, high compressive strength, moderately high heat and fire resistance capacity, low cost and ease of mouldability to various shapes. In the construction industry, concrete is still one of the prime materials in use, from building a foundation to structures like buildings, bridges, tunnels, deep underground basement-type structures, dams, retaining walls, and underground parking lots. However, the main flaw in conventional concrete lies in the risk of crack formation due to various reasons like shrinkage, tension, fatigue loading, and even environmental conditions.
Crack formation in concrete can occur in both plastic and hardened states. During the plastic state, the main factors leading to crack formation are formwork removal, plastic settlement, and plastic shrinkage caused by rapid water loss from the concrete surface. On the other hand, drying shrinkage, temperature stress, unaccounted external loading, sustained overloads, weathering, errors in design and detailing, and harsh chemical exposures result in crack formation within the concrete and surface cracks in the hardened state [1]. These micro-cracks can reduce the concrete strength as well as increase permeability, thereby initiating corrosion in the reinforcement embedded within the concrete, which can, in the long run deteriorate concrete’s structural integrity, durability, and thereby its life span. To mitigate such problems in concrete, self-healing concrete can be considered an actual solution well within the service life of the concrete. The crack-filling mechanism provides an eco-friendly solution to prevent the rebars from corroding. Also, sometimes accessibility to the cracked zone becomes a problem, due to which the micro-cracks might be overlooked. In such cases, self-healing mechanisms in concrete also offer an effective solution in filling those micro cracks. The process imitates the automatic healing of body wounds by various mechanisms, and that’s why the name – is “Self-Healing”.
Autogenic Self-Healing in Concrete
The inherent healing potential in concrete makes it capable of healing cracks in any ordinary concrete element, called autogenic self-healing. But this crack healing capacity is limited as well as unpredictable. It has been observed that complete healing of fine cracks is possible under moist conditions, mostly due to delayed hydration of the un-hydrated cement in young concrete and sometimes due to carbonation in the old concrete.
(a) 100% PC cement mix and (b) cement with expansive minerals
Figure 1[3]: ─ The typical crack sealing pattern in 28 days:
Various studies have shown that this delayed hydration process can further be enhanced with the use of blast furnace slag or fly ash blended with Portland Cement [2] or by using optimum supplementary cementitious materials (SCMs), Smart Expansive Minerals [3] and crystalline admixtures. Figure 1 shows photographs of autogenic healing patterns in 28 days for both normal concrete and expansive minerals. The mechanism behind such a healing process is to produce calcium carbonate (CaCO3), which is highly compatible with the cementitious composites, to fill in the cracks, which may be explained as follows:
Step-1: Carbon dioxide dissolves in water, releasing HCO3¯ & CO32-
H2O + CO2 è H2CO3 è H+ + HCO3¯ è 2H+ + CO32-
Step-2: Cement hydration releases free calcium ions dissipated through concrete and the cracking surfaces. These calcium ions react with HCO3¯ & CO32- forming CaCO3 crystals.
Impurities also block some cracks in concrete in the presence of water or by swelling the hydrated cementitious matrix (calcium silicate hydrate gel) in the crack flanks [4]. Internal stress within the concrete element and the curing conditions can significantly affect autogenous self-healing in concrete. If, under curing conditions, the crack face comes into contact with a specific amount of impelled compressive stress, better crack healing may be obtained [3].
Studies have also been carried out using Fibres of different materials, both natural and manmade, to enhance autogenic healing by restricting crack width. Natural fibres used in concrete may be obtained from plants and animals, such as coir, wood, flax sisal, wool, etc. Fibre-reinforced concrete technology also includes using industry-manufactured fibres like polyester, polypropylene, polyethene, asbestos fibre, ethylene vinyl alcohol, polyvinyl alcohol, etc., called synthetic fibres [5]. Synthetic fibres improve concrete’s tensile strength and toughness by controlling the plastic and drying shrinkage cracks and forming a better bond within the concrete matrix. Also, the permeability in concrete is reduced by this crack-controlling mechanism, which prevents water penetration through pores and improves the mechanical properties of the concrete.
The stress generated by the Shrinkable polymers while shrinking under a specific condition may be effectively used in crack closure and, thereby, self-healing. When polymers like polyurethane, having elastic properties, are added to the concrete mix, they bond with the cement particles and a layer of polymer net is formed to repair the cracks [5]. Such bonding between the polymers and mortar improves during the shrinkage of polymers and improves the mechanical properties of concrete. The higher viscosity of the polymers enables the effective filling of cracks. In a project by the Cardiff University research group [6], a shrinkable polymer polyethene terephthalate (PET) with a nickel-chrome wire heating system was introduced inside the concrete structural element. The tendons were activated by passing a current through the wires wrapped around them, heating them. The autogenous self-healing process was enhanced by the compression induced due to the activation of the polymer tendons, which helped the crack closure.
Crystalline Admixtures (CA) are a special type of permeability-reducing admixture (PRA), as reported by the ACI 40 Committee 212 [7]. Being hydrophilic, these materials react easily with water. Such reactions result in the formation of water-insoluble needle crystalline deposits that block pores/cracks, thereby increasing the density of Calcium Silicate Hydrate (CSH) and resisting water penetration. Depending on the crystalline promoter, a modified CSH precipitates from the calcium and water molecules due to the reaction between the active chemicals within cement and sand. According to some researchers, tricalcium silicate (C3S) and water react with CA, while others indicate a reaction with calcium hydroxide (CaOH), resulting in crystal formation. Also, these admixtures are capable of producing more hydrated products to fill the cracks within the concrete matrix, during and post hydration. This helps improve the mechanical properties of the concrete and strength regaining [8].
Figure 2[9]: ─ Crack sealing patterns under the water curing condition
In comparative studies between concrete with CA and concrete with other expansive admixtures, it was shown that improved self-healing might be obtained using crystalline admixtures, than other types of additions in the range of smaller crack widths. But the same admixtures became inefficient for wider cracks. While cracks of width 0.1 mm may completely heal after around 200 hours, the cracks ranging from 0.15 to 0.3 mm in width significantly decrease in 7 days and completely heal in 33 days [10]. Again, a combination of CA with expansive admixtures achieved complete self-healing for cracks up to 400 microns after 30 days of curing [2].
The above studies show that moisture is necessary for normal concrete and concrete with CA (Refer to Figure 2). It is also observed that at 42 days of curing, the best crack sealing could be achieved, which may be attributed to the delayed hydration process in concrete. Studies with crystalline admixtures have shown complete healing of early-age cracks and structural cracks in concrete elements under the submerged condition and cyclic dry-wet exposures, while such cracks were only partially healed under air exposure. Also, the behaviour of these products, with other elements in concrete, still needs to be discovered.
The following factors influence autogenous self-healing in concrete:
- Time of curing: A longer hydration can yield better self-healing performance.
- Water–cement ratio: A higher water–cement ratio enables the hydration of more unreacted cement particles, boosting the calcium carbonate generation in the concrete matrix, thereby enhancing the self-healing in concrete.
- Moisture content: The presence of water is required for almost all autogenous self-healing techniques except some using fibres and polymers.
- Crack width: Complete healing is possible for smaller crack widths, and with increased crack width, the self-healing efficiency drops rapidly.
- Stress: Better self-healing may be obtained in the concrete elements by loading proper pressure (compression) on the cracks.
Figure 3[3]: ─ Self-healing concrete systems.
Figure 3 gives a tabulated description of various self-healing technologies. Although some researchers have considered using such fibres, polymers, and mineral admixtures as a stimulated autogenous healing technique, others have grouped them under autonomous self-healing systems, described in the subsequent section below. However, autogenic healing cannot be considered a reliable phenomenon to obtain significant healing effects in concrete as only a limited quantity of healing products is formed in this process. Further, it is effective for smaller crack widths (up to 300 μm) [10] & [11], and the performance is at an early age due to the presence of more un-hydrated cement.
Autonomic Self-Healing in Concrete
In recent years, several new “engineered healing concepts”, called autonomic self-healing systems, have been investigated, by incorporating material components not traditionally used in the concrete. These systems use a microvascular network or capsules filled with healing agents, which may be polymer gels or microorganisms like bacteria. Autonomic self-healing in concrete may be achieved when such healing agents are released from a reserved encapsulation or a continuous vascular network. Even after complete hydration, 20 to 30% of cement remains un-hydrated, which can be used by these healing agents to form an effective crack-filling compound.
Figure 4[4]: ─ Crack-healing mechanism using vessels (above) & microcapsules (below) containing healing agent
Figure 4 demonstrates how the healing agents are released from the vascular network and microcapsules during the crack-filling process. Healing agents are epoxy resins, cyanoacrylates (super glues), alkali-silica solutions, methyl methacrylate, expansive minerals, hydrogel, etc. Sodium silicate is considered a promising healing agent for encapsulation [12]. Healing agents are to be chosen, so their viscosity is less to cover a longer crack path in the damaged area, and microcracks in a wider area may be filled in. Healing agents should also have a strong bondability to bind the crack faces. T. Qureshi reported considerable strength recovery performance with such healing agents within the crack range between 300 and 500 μm [3].
Common encapsulating shell materials are glass, ceramic, polymers and lightweight aggregates. Even clay pellets are used in some cases [3]. Chemical encapsulation is the most popular choice due to its versatility. Various types of healing agents can be encapsulated in a variety of shapes & sizes. Since the healing mechanism is independent of the external environment, it can be used in various infrastructures where accessibility is an issue. Also, the capsules can be mixed directly into concrete, making this technique more appealing than the others. However, the capsules shall be so manufactured that they can uniformly disperse within the concrete. These are strong enough to withstand the mixing process and transportation, and the capsule material does not react with the concrete ingredients, including admixtures and superplasticisers. Also, the capsules replacing aggregates in considerable volumes, hurt the mechanical strength of concrete. In a research project at Cambridge University [13], polymeric microcapsules filled with a liquid sodium silicate core were combined with different kinds of commercially available repair mortars to prove compatibility regarding fresh properties and mechanical strength to increase self-repairing performance.
A vascular network is a tubular system formed with Capillary glass tubes (Refer to Figure 5) to carry the healing agent into the concrete matrix. The diameters of the glass tubes used in different projects vary within a range of 0.8 mm to 4 mm [3]. The glass tubing is filled with the healing agents that fracture when a concrete crack is intercepted, releasing the repair chemical for crack filling. The vascular networking system may be considered an alternative variant of chemical encapsulation for delivering the healing agent within the concrete matrix. Though it poses certain difficulties in casting, it can potentially carry more healing agents than microcapsules. Also, it is possible to link these tubes to external glue sources, which is termed an active mode of self-healing [4].
Figure 5[3]: ─ (a) Vascular network in concrete slab panel & (b) Vascular network combination with PET in field trial
In a recent field trial of a road improvement scheme [3], vascular network systems were combined with shape memory polymer tendons (PET) (see Figure-5(b)) in large-scale structural elements, and promising healing performance was obtained. Shape memory polymers are a class of smart materials that can be stored in simple temporary shapes by material immobilisation and can return to their equilibrium shape, which is more complex if triggered by an external stimulus [14]. Though no studies could be found with more than one loading cycle, however from the action mechanism, it can be apprehended that repeatability of healing at the same region may not be possible in healing by chemical encapsulation or vascular network, since the capsules or tubes at any region once emptied during the first damage cycle, cannot be refilled.
Alkali-resistant endospore-forming bacteria of Bacillus and other species, that precipitate calcite – a suitable filler for concrete, through biological metabolism are used in concrete as a self-healing technology. The process involved in calcite production is termed microbiologically induced calcite precipitation (MICP), which can be either urea and urease based or calcium-lactate-based [3]. In this process, calcium carbonate is generated by bacteria metabolism in a high-calcium environment, and a nutrient is also required to feed the bacteria.
Microorganisms produce carbonate extracellularly through autotrophic and heterotrophic pathways [1]. In the autotrophic pathway, the microbes absorb carbon dioxide and convert it to carbonate. The heterotrophic pathway occurs when the microbial communities precipitate carbonate mineral crystals due to their Heterotrophic growth on organic salts. These bacteria, such as Bacillus, Arthrobacter, and Rhodococcus species, use organic compounds as a source of energy [1]. Calcium carbonate and Magnesium carbonate crystals are produced, based on the salts and carbon sources present in the medium.
Bacteria and nutrients can be added directly to the fresh concrete mix. However, the bacteria cannot survive long in the alkaline environment of fresh concrete and the dry conditions of hardened concrete. The increase in pH value reduces bacterial activity and growth considerably. Accordingly, encapsulation of bacterial spores or insertion through the vascular network are recent developments in this field. The microcapsules shall be uniformly dispersed in the concrete mix and suitable for mixing and transportation. They shall be manufactured to be flexible in moist conditions but become brittle on drying or when exposed to a cracked face. With this kind of bacterial encapsulation system, crack widths up to 970-μm were healed successfully, four times greater than the non-bacterial mixes [3]. While using the vascular networks to distribute the microorganisms, the material of tubes should be such that it can withstand the alkalinity of the green concrete and become brittle with the age of concrete to rupture at the crack interface. However, the activity and viability of bacteria in hardened concrete for a prolonged period need further investigation.
Temperature and Other Environmental Influences
Studies have also shown that the self-healing capabilities of concrete containing microcapsules of various materials have considerably increased with the rise in temperature from 10 °C to 50 °C [15]. An application in 2014, used bacterial self-healing concrete in an irrigation canal in Andean Heights, Ecuador, where the casting was done at a temperature of 5°C [16]. But, for higher temperatures, the self-healing performances would depend on the capsule materials.
The durability of concrete is strongly affected under chlorides and sulphate exposures. The sulphate attack forms expansive and strength-reducing products, directly degrading concrete’s overall properties. On the other hand, chloride attack initiates corrosion of the reinforcement steel and indirectly deforms the concrete element. Specimens submerged in marine water [17] have shown better overall healing than similar specimens submerged in fresh water. However, as explained earlier, this study also showed that the healing efficiency depends on the initial crack width and decreases with an increase in the initial crack width. Best healing was observed in marine water specimens, with complete healing in cracks up to 0.72 mm initial [17]. However, such self-healing performance may be attributed to the fact that the specimens were continuously submerged as the performance was reduced under tidal conditions.
Studies concerning the effect of atmospheric sulphate or chloride on self-healing materials still need to be completed. Research is necessary to find short- and long-term effects. Similarly, the effect of the various self-healing materials on the reinforcement steel must be carefully studied.
Effect of Admixtures
Various admixtures like accelerators, retarders, plasticisers, etc., are commonly used for concrete production, and much knowledge advancement occurred in this field. Increased use of High strength concrete and High-performance concrete resulted in the mandatory use of admixtures. Considering these factors, it is very important to assess the effect of admixtures on self-healing materials. A literature survey reveals the absence of studies and data in this important area, and further experimentation is felt imperative for acceptability, except in limited specific applications where admixtures are not used.
Performance & Cost
Studies have compared the performance of the different self-healing technologies described above, and the evaluation results are highlighted in Table-1 [18], which has been named the “Robustness Matrix” by the authors. From this matrix, it may be noted that the current literature does not contain adequate data to assess this technology’s quality, reliability, repeatability and applicability. In almost all self-healing investigations, only a limited number of specimens are used, and that too, mostly mortar specimens without any reinforcement. Even though some researchers used large-scale elements (especially beams) with practical dimensions, what cannot be ignored is the fact that they were still carried out in a lab environment under controlled conditions and loadings.
Table 1[18]: Robustness matrix of self-healing approaches.
Even though self-healing concrete has seen very limited field application to date, a few examples can still be identified. Antwerp, Belgium, a roof slab (3.9m below ground level) of an underground inspection chamber was cast with bacterial self-healing concrete [19]. Since 2013, a bacterial repair mortar has been applied in the Netherlands as patch repair in different locations and under diverse weather conditions [16]. In India, Nuclear Power Corporation started researching bacterial concrete for using such technology in nuclear power plants [20].
As estimated in the last decades, in Europe, around 50% of the annual construction budget is spent on the repair & rehabilitation of existing structures [21]. In a 2012 journal [18], the annual economic impact associated with maintenance/repair and replacement of deteriorating structures was estimated at $18-21 billion in the U.S. alone. The same paper also quoted – “The American Society of Civil Engineers estimates that $2.2 trillion is needed over the next five years for repair and retrofit; a cost of $2 trillion has been estimated for Asia’s infrastructure.” Again, such repairs of concrete structures are often short-lived, further worsening the cost implications. 55% of EU repairs reportedly fail within five years of service life [13].
Undoubtedly, such maintenance requirements of concrete infrastructure over their service life put a question mark on their sustainability, and hence over the past few decades, self-repairing techniques with minimum human intervention have come up as a possible cure. Further, the cement manufacturing industries contribute significantly towards global carbon emissions. Accordingly, apart from the economic cost of repair and rehabilitation, other important points of concern behind such infrastructure deterioration, are the social and environmental costs which are apparently ignored due to very limited quantification and documentation.
Figure 6a[21]: ─ Performance and cost, including direct repair cost, versus elapse time for (A) Normal concrete infrastructure (B) High-quality concrete infrastructure
Figure 6b[21]: ─ Performance and cost versus elapse time for structure built with self-healing material
To compare the performance of both normal concrete and self-healing concrete concerning the overall expenditures for initial preparation and subsequent maintenance, Van Breugel (2007) presented graphs [21] describing the performance of structures with time elapsed. In Figure 6a, it is observed that gradual degradation occurs after the formation of initial cracks, until the moment when the first repair is required urgently. Even after the repair, the structure’s durability still cannot be ensured as very often, a second repair is needed within another ten to fifteen years [21]. Accordingly, it is obvious that much of the expenditure is borne towards the repair and maintenance works for normal and high-quality concretes.
However, the onset of repair requirements can be delayed considerably with the application of self-healing technology in concrete, which involves more initial investment. Self-healing gives a longer material lifespan with lesser inspection, reducing maintenance costs. The ideal case, as depicted in Figure 6b above, would be that after the initial expenditure of self-healing concrete, no more cost is required for repair and maintenance works as the material will repair itself. Having said this, it cannot be denied that the self-healing concrete cost is considerably high for normal construction use. According to the latest research [22], using bacteria-infused self-healing concrete, the price can increase to $6,000 per cubic meter compared to normal concrete, which is available at around $150 per cubic meter. However, such high cost may be attributed to the type of bacteria used and that too procured in very limited quantities for mortar sampling only.
Since no other reference could be identified validating the cost of any of the self-healing techniques discussed above, it would be unrealistic to generalise the cost of self-healing concrete at such a high value. Moreover, considering the ingredients used, it is expected that the cost of these self-repairing systems will decrease when produced in bulk quantities and with further advancement of technology.
Overview of Market Potential
As per a market analysis report by Grand View Research [23], the global self-healing concrete market size was valued at USD 24.60 billion in 2019, and from 2020 to 2027, it is expected to expand at a compound annual growth rate (CAGR) of 37.0%. Figure 7 shows the growth forecast for the U.S. market from 2016 to 2027.
Figure 7[23]: ─ U.S. self-healing concrete market size, by form, 2016 – 2027 (USD Million)
As per the report, the market demand for self-healing concrete in 2020 was 338,000.0 cubic meters, which is forecast to grow to 6,672,347.1 cubic meters in 2027. This growing demand over the forecast period is expected to be driven by the constantly increasing demand for sustainable constructions in all applications, namely, infrastructure, industrial, residential and commercial. As the construction industry’s growth is rising globally, demand for low-maintenance structures is inevitable, which may further support the market growth of self-healing concrete.
The application-wise share of the Global self-healing market in 2019 is given in figure 8. The infrastructure application segment held the largest share of 58.3% in revenue and is likely to grow significantly over the forecast period [23]. Due to heavy-duty operations, the industrial structures withstand harsh process impacts, including heat and chemical treatments that require rigid and durable surfaces without compromising safety. Hence, self-healing concrete is expected to grow in this area. As projected in the said report, self-healing concrete will also be used in residential and commercial buildings in the future years to manage cracks and thereby give better waterproofing solutions. However, 2020 saw the COVID19 pandemic globally, especially in the first two quarters, which adversely impacted the overall construction business and subsequently hampered the market for the product [23].
Figure 8[23]: ─ Global self-healing concrete market share, by application, 2019 (%)
Conclusion
Concrete is one of the most used and economical construction materials in various industrial structures; damage and failure within the design lifetime of a structure is a threat to such industries. The compressive strength and other mechanical properties of concrete can substantially decrease due to the formation of cracks in hardened concrete. Also, crack formation increases the concrete permeability, thereby inducing reinforcing steel corrosion and reducing the structure’s durability. Self-healing concrete has great potential to mitigate these challenges.
All the self-healing techniques may be found effective under certain laboratory conditions and for smaller crack widths (<1mm) in both new and old concretes. However, the limitations in the various approaches require further investigation before the vision of self-repairing concrete can be fully realised in practical applications. While autogenous healing requires water exposure in most cases, the autonomous techniques’ main drawbacks are workability issues, sometimes worsened mechanical properties, the endurance and performance of capsules and bacteria in the adverse concrete environment, very high price, and lack of full-scale evaluation. Common grey areas for both techniques are unassured healing efficiency, whose extent cannot be estimated.
Depending on the use and exposure conditions, different codes have limited the crack width to 0.1 to 0.3mm. To meet the stipulated crack width guidelines, often additional reinforcement is required in design, thereby increasing the overall concrete cost. The use of self-healing concrete, which is more effective in case of such smaller cracks, can do away with the additional reinforcement reducing the cost of reinforcing steel. However, extensive studies on real-life structural elements with self-healing concrete are to be carried out to ensure that the crack width is limited within the guided range through a long-term duration, before implementing such application into the codal provisions.
All said and done, the major challenges for all self-healing concrete in the construction industry lie in the considerably high additional expenditure, the performance validation regarding long-term durability and the lack of large-scale applications. Climate changes and global warming are the major issues that must be addressed in all futuristic solutions. Innovations, research and experimentation need to be vigorously pursued to achieve excellence and bring new materials and technologies. Self-healing concrete has the immense potential to be a sustainable solution by reducing the usage of high embodied energy materials like cement and steel and reducing construction and demolition wastes. Hence, it is worth continuing the research and development in this field to bridge the gaps mentioned in the previous discussions and reduce the cost to a reasonable level, given the projected market potential.
References
- “Bioconcrete: next generation of self-healing concrete” by Mostafa Seifan, Ali Khajeh Samani, Aydin Berenjian, School of Engineering, Faculty of Science and Engineering, The University of Waikato, Hamilton, New Zealand.
- “Self-healing capability of concrete with crystalline admixtures in different environments” by M. Roig-Flores (marroifl@upv.es), S. Moscato, P. Serna, L. Ferrara, Construction and Building Materials. 86:1-11, http://dx.doi.org/10.1016/j.conbuildmat.2015.03.091.
- “Self-Healing Concrete and Cementitious Materials” by Tanvir Qureshi (qureshi@utoronto.ca), University of Toronto, Canada and Abir Al-Tabbaa, University of Cambridge, UK, http://dx.doi.org/10.5772/intechopen.92349
- “A Review of Self-healing Concrete Research Development” Amirreza Talaiekhozan, Ali Keyvanfar, Arezo Shafaghat, Ramin Andalib, M.Z Abd Majid (mzaimi@utm.my,), Mohamad Ali Fulazzaky, Rosli Mohamad Zin, Chew Tin Lee, Mohd Warid Hussin, Norhaliza Hamzah, Nur Fatimah Marwar, H.I. Haidar, Journal of Environmental Treatment Techniques, 2014, Volume 2, Issue 1, http://www.jett.dormaj.com.
- “Effect of crystalline admixtures, polymers and fibers on self-healing concrete – a review” by C. Manvith Kumar Reddy (manvithkumarreddychitiki@gmail.com), B. Ramesh, Dannie Macrin, Materials Today: Proceedings, https://doi.org/10.1016/j.matpr.2020.06.122.
- “A shape memory polymer concrete crack closure system activated by electrical current.” By Teall O, Pilegis M, Davies R, SweeneyJ, Jefferson T, Lark R, et al in Smart Materials and Structures. 2018, https://www.annualreviews.org/doi/10.1146/annurev-matsci-082908-145419.
- “Report on chemical admixtures for concrete.”, ACI Committee 212, 2010, American Concrete Institute (ACI), Chapter 15, pp 46-50
- “Macro mechanical properties of self-healing concrete with crystalline admixture under different environments” by T. Chandra Sekhara Reddy (ce@gprec.ac.in), A. Ravi Theja, GPR Engineering College, Kurnool, India, https://doi.org/10.1016/j.asej.2018.01.005
- “Self-Healing Ability of High-Strength Fibre-Reinforced Concrete with Fly Ash and Crystalline Admixture” by T. S. Reddy (tcsreddy61@gmail.com), A. R. Theja, C. Sashidhar, Materials Science, Engineering, Civil Engineering Journal, Vol. 4, No. 5, May, 2018, http://dx.doi.org/10.28991/cej-0309149
- “Self-healing Concrete” by Xu Huang, S. Kaewunruen (kaewunruen@bham.ac.uk), University of Birmingham, New Materials in Civil Engineering, 2020, Elsevier.
- “A Review of Self-healing Concrete for Damage Management of Structures” by Henk Jonkers (m.jonkers@tudelft.nl), Technische Universiteit Delft, Delft, Netherlands.
- “New Sustainable materials for Construction” by R L Dinesh, TATA Consulting Engineers Limited.
- “Development of sustainable concrete repair materials via microencapsulated agents” by Chrysoula Litina (cl519@cam.ac.uk) and Abir Al-Tabbaa, Engineering Department, University of Cambridge, UK, in MATEC Web of Conferences, Concrete Solutions 2019, https://doi.org/10.1051/matecconf/201928911002
- “Shape Memory Polymer Research” by Patrick T. Mather (rousseau@gm.com), Xiaofan Luo (xluo06@syr.edu), Ingrid A. Rousseau (ingrid.rousseau@gm.com), Annu. Rev. Mater. Res. 2009. 39:445–71, https://www.annualreviews.org.
- “Effect of temperatures on self-healing capabilities of concrete with different shell composition microcapsules containing toluene-di-isocyanate” by Wei Du, Jianying Yu (jyyu@whut.edu.cn), Shunjie Gu, Ruiyang Wang, Jiangting Li, Xiaobin Han, Quantao Liu, https://doi.org/10.1016/j.conbuildmat.2020.118575.
- Science Direct Topic – Bacteria Based Concrete, 2018 https://www.sciencedirect.com/topics/engineering/self-healing-concrete
- “Characterisation of autogenous healing in cracked mortars under marine water exposure” by Muhammad Basit Ehsan Khan, Luming Shen (shen@sydney.edu.au), Daniel Dias-da-Costa, Magazine of Concrete Research 2020, https://doi.org/10.1680/jmacr.20.00162
- “Robust Self-Healing Concrete for Sustainable Infrastructure”, by Victor C. Li (vcli@umich.edu), Emily Herbert, Journal of Advanced Concrete Technology, volume 10 (2012), pp. 207-218, Japan Concrete Institute, https://www.j-act.org
- “First Large Scale Application with Self-Healing Concrete in Belgium: Analysis of the Laboratory Control Tests” by Tim Van Mullem, Elke Gruyaert, Robby Caspeele and Nele De Belie (DeBelie@UGent.be), Materials 2020, 13, 997; https://www.mdpi.com/journal/materials
- “Self-Healing Concrete” by Shubham Sunil Malu, https://www.engineeringcivil.com/self-healing-concrete.html
- “Addressing Infrastructure Durability and Sustainability by Self Healing Mechanisms – Recent Advances in Self Healing Concrete and Asphalt” by Erik Schlangena (E.J.G.Schlangen@tudelft.nl), Senot Sangadji, The 2nd International Conference on Rehabilitation and Maintenance in Civil Engineering, https://www.sciencedirect.com
- “Can Concrete Heal Its Own Cracks Without Losing Its Strength?” reported by Avni Shah, in 2022, https://viterbischool.usc.edu/news/2022/03/can-concrete-heal-its-own-cracks-without-losing-its-strength/
- “Self-healing Concrete Market Size, Share & Trends Analysis Report By Form (Intrinsic, Capsule Based, Vascular), By Application (Residential, Industrial, Commercial, Infrastructure), By Region, And Segment Forecasts, 2020 – 2027”, https://www.grandviewresearch.com/industry-analysis/self-healing-concrete-market