Captive Co-generation Plants: Selection of optimum configuration – Key to Success
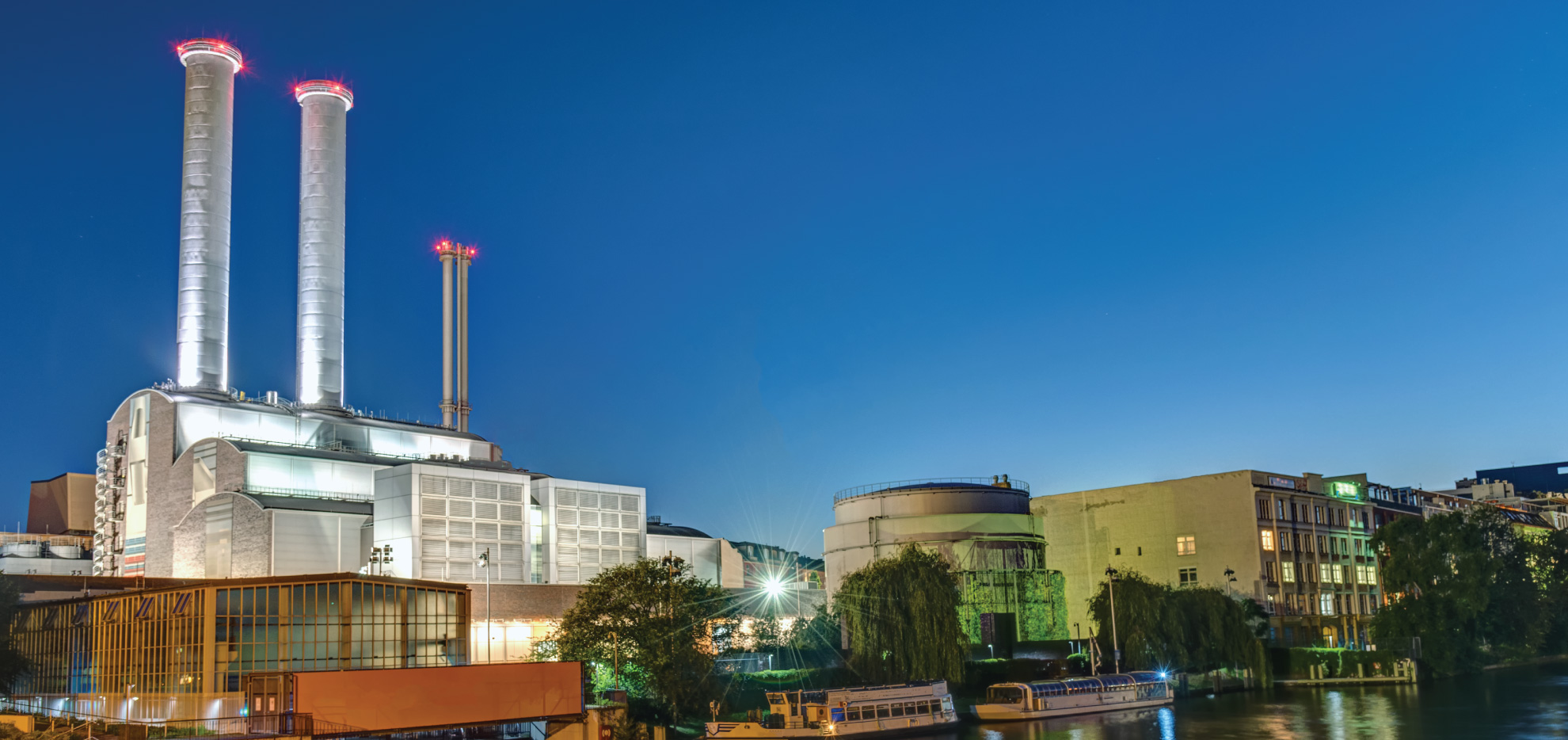
Large process plants typically demand both power and process steam at multiple pressure levels. While power demand can be met by either in-house generation or from grid or in combination of both, process steam is generated in-house. Selecting the most optimum configuration to meet the process plants’ demand of generating in-house process steam and power either partly or full is always a challenge to the captive plant designers and requires thorough knowledge and experience of process steam/power generation mechanisms and also overall understanding of process dynamics as every co-generation plant is unique and demands customized solution
Hence, replicating co-generation plant configuration from another plant or from existing plant in case of expansion projects could be counterproductive as it may lead to uneconomic plant operation and at times may adversely affect the process plant performance as well.
Majority of the large process plants demand both power and process steam at multiple pressure levels. Requirement of both power and process steam are large and variable. As the plant’s operation depends on the supply of power and process steam, the generation of power and steam must be steady, uninterrupted and at the same time able to cope up with varying demands of process plant.
Typically process steam is generated in-house as steam transportation from distance is never a feasible solution. Generation of power on the other hand depends on multiple factors such as
- Variation in load demand with time & peak power demand
- Economics, reliability and constraints (if any) of power supply/purchase from utility grid
- Optimum utilization of facilities that are otherwise required for process steam generation to generate power as well (co-generation)
- Minimum un-interrupted power supply to sustain critical loads even during emergency
- Cost economics of purchasing power from grid and generating power in-house without violating technically imposed limitations dictated by process plant’s requirements
In case of expansion of existing process plant, the existing facilities and site constraints also to be considered in addition to the points indicated above to arrive at the most optimum solution
Every co-generation plant is unique as its type, configuration, redundancy, fuel etc. varies to suit the multiple demands of the process plant. As such optimum design of a co-generation plant needs thorough understanding of power and steam generation process and also the need for power and steam by process plant under all possible operating conditions including abnormal/ emergency conditions.
Such multi directional demands and multiple options of plant configuration pose a huge challenge to plant designers to select the most optimum plant configuration. TCE has a wealth of knowledge and experience in conceptualizing and designing such co-generation systems both in domestic and in international arena.
In one recent project engineered by TCE, as part of expansion program of existing steel plant, additional power and process steam were required to meet the demand of expansion program.
This steel plant has 7 coal/coke oven gas fired boilers and 5 waste heat boilers of varying capacity and steam parameters operating in tandem with 2 back pressure and 1 extraction condensing steam turbines along with PRDS to supply power and process steam for the entire complex.
TCE first studied the increase in power and steam demand and reconfirmed the requirement of steel plant through detailed discussions with O& M personnel of various units of the steel plant, reworked the additional requirements and submitted to the customer for their concurrence. Simultaneously, the conditions of the existing steam and power generating units were studied to understand and evaluate their capabilities of generating steam/ power on a long term basis under varying operating scenario. Duly considering these aspects, actual requirement of additional power and steam that need to be met by installing new power/steam generating units to support steel plant expansion program was worked out.
Steel plant expansion included installation of waste heat recovery boilers integral to coke dry quenching (CDQ) units. With additional steam availability from proposed CDQ units, overall steam and power balance carried out duly considering unit outages so that under no circumstances the steel plant should be starved of steam supply (first priority) followed by power supply with grid power as back up.
While doing this exercise, the assessment of existing facilities to bear the additional loads (for ex. Limitation in existing pipe supporting structure to take additional load imposed a limitation on the quantity of additional steam that can be transported) and other physical constraints in terms of steam pressure/ temperature drop etc. were also given due weightage.
A total of 54 possible options were identified. This list of options then studied at global level and pruned to 10 most feasible options for further study. Finally based on performance benefit, ease of execution and cost consideration the most optimum option was selected.