Failure Modes and Effects Analysis (FMEA) as a Reliable Tool for Sustained Operations
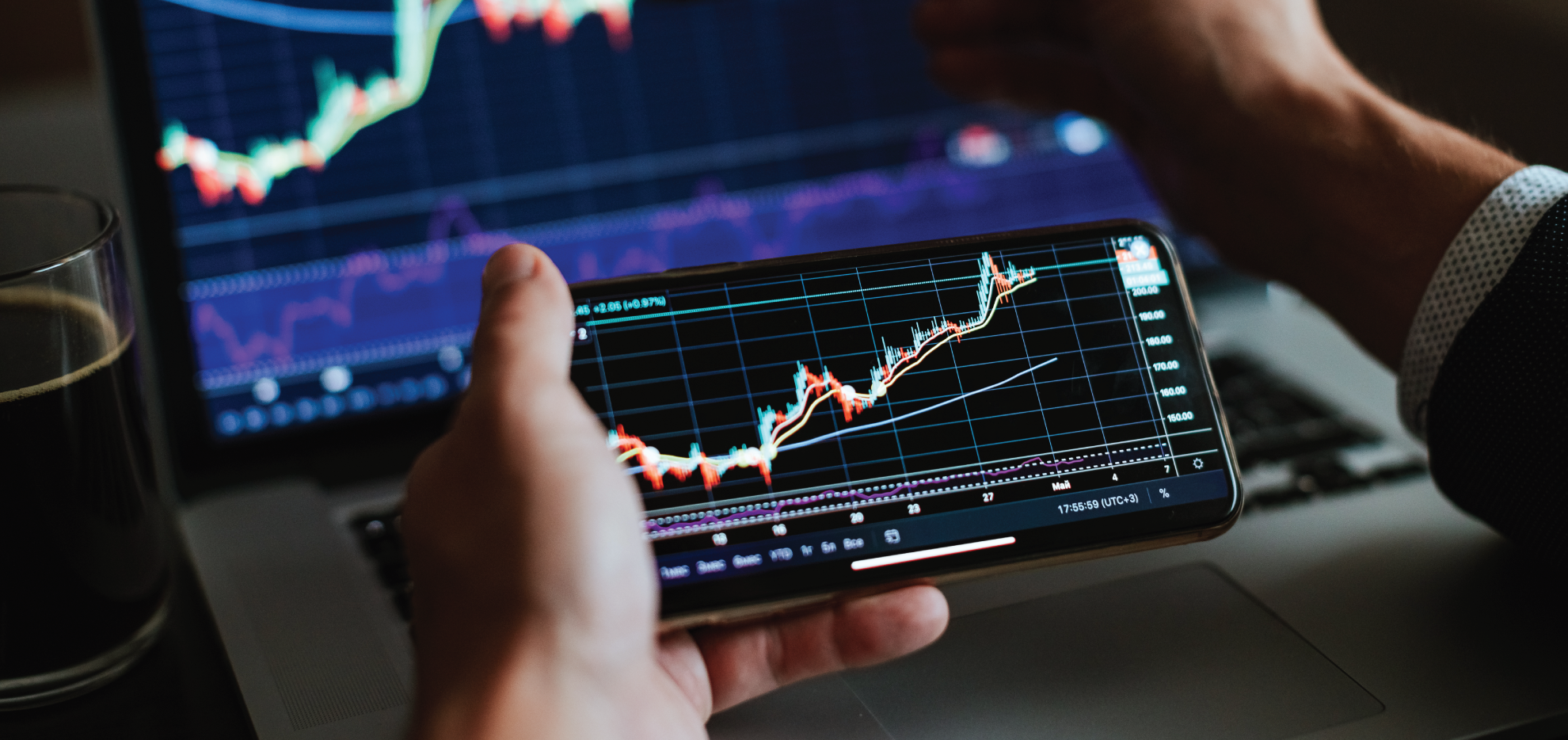
In today’s world, ensuring plant reliability & availability is the key to sustain industries.
Good news is, informed plant owners / O&M contractors are therefore today commissioning FMEA based Single Point of Failure (SPoF) or gap analysis before they take over. FMEA is a systematic method for evaluating a process to identify where & how it might fail and to assess the relative impact of different failures. It is a means to assess the risk associated with those failure modes, to rank the issues in terms of impact, to identify and carry out corrective actions.
In power and process Industries today, FMEA is being increasingly used for “Gap Analysis” for the equipment/systems and facilitate implementation of mitigation measures to bridge the gaps. There are specific cases where the O&M contractor commissions a SPoF study to identify any single piece of equipment or function that, if fails, could cause generation/production loss and de-rating of the Contracted Capacity.
In one such recent assignment executed by TCE , for a large capacity Combined Cycle Power Plant (CCPP) project under final stages of construction in KSA, , FMEA based Gap Analysis with SPoF study & costing for mitigation implementation was performed on behalf of O&M contractor selected to take over plant O&M.
Time available was short considering the enormous amount of data /drawings needed to be studied. . Not much help from site team, neither from EPC contractor was available as they were busy in construction and pre-commissioning activities and the onus of providing the solution in its entirety was on TCE. This was a challenge since enormous design and site data had to be sifted to find gaps and interaction with EPC for clarifications was not possible.
The job was executed through desk top study, followed by site visit, study of design data & drawings and subsequent VCs. The key thing which worked for TCE was our system knowledge gained through immense experience in designing similar plants.
First step was to get the buy-in from customer for the list of items/systems to be covered under the study. Equipment and system design gaps were identified through detailed FMEA analysis for nine (9) main plant groups and tabulated. They were categorized as High, Medium and Low risk items based on probability & impact.
Minimum two (2) mitigation options were identified and recommended for each Gap. Options had to be prudently selected for High, Medium and Low Risk categories. Practicability, cost, timelines and overall impact were the key items. Potential RPN (Risk Priority Number) was identified for each gap. Reduced RPNs were identified for each of the recommended mitigation options to enable customer to make a practical choice.
Around 20 high Risk items were identified and successfully presented to Project Owner, to highlight the impact of the same on plant performance & generation, if not mitigated.
Such Gap Analysis requires, thorough knowledge and expertise to understand the plant process, the design philosophy, plant operating criteria, and successful execution of such projects demonstrates the capability & expertise that lies within TCE.