Steam Audit: A case study
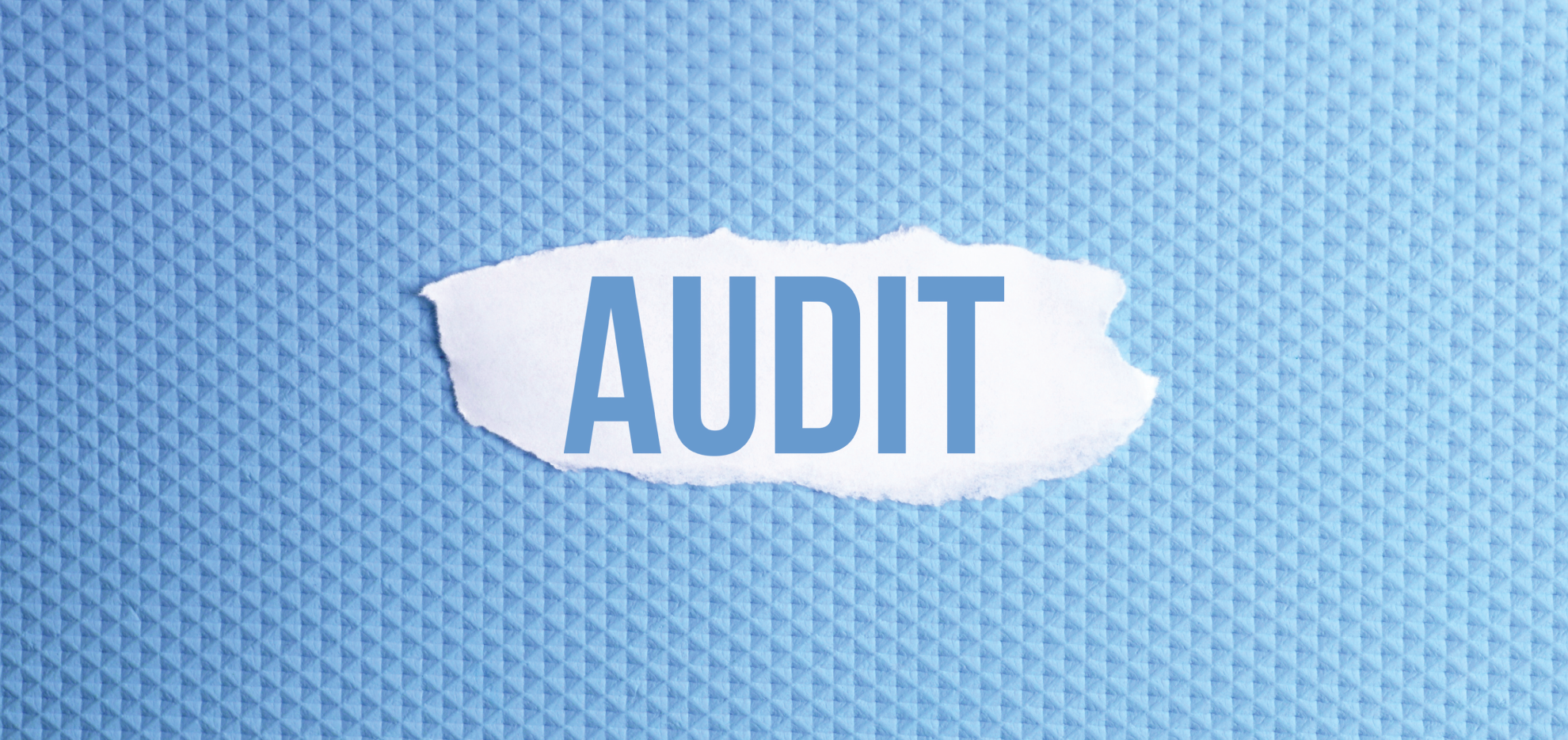
Energy cost is one of the significant contributors of production cost for most of the Industries. Hence, reduction in energy consumption electrical, thermal or in any other form always helps in business sustenance and growth. Moreover, as most of the energy is derived from fossil fuels, any reduction in energy consumption would also mean conservation of natural resources and most importantly less environmental impact.
Typically energy conservation happens in 4 steps:
a) Compare present specific energy consumption (SEC), i.e., energy consumption per unit rate of production with benchmark SEC for the applicable industry
b) Study and understand the existing mechanisms of energy consumption as well as avoidable energy losses, etc.
c) Prepare the list of action items recommended to improve SEC and prioritise them in accordance with their impact on SEC, cost of implementation, difficulty/ease of implementation and overall economics
d) Set out a road map for implementation of recommendation
e) Implement as per recommendation
Steps (a) to (d) are covered in energy audit which could be comprehensive audit encompassing all forms of energy used in the industry or only specific to one particular energy, viz. electric energy audit, steam audit, etc.
Steam is one of the major forms of energy used in industries like refineries, pulp & paper, metal industry, fertiliser, petrochemical, thermal power plants, etc. Hence, steam audit is important for such industries with high specific steam consumption (SSC).
The need for steam audit is gaining further importance with increasing energy and water cost.
Audit of steam system covers aspects such as study of:
a) Steam generation (Boiler including HRSG/WHRB)
b) Steam distribution system
c) Steam leaks & steam traps
d) Steam condensate system
e) Steam system thermal insulation
Here is a case study of steam audit of a typical Oil Refinery done by TCE
Methodology adopted for the study was:
a) Understanding the existing system by:
i) Safety training for the engineers assigned for site survey
ii) Visit by audit team for familiarization with hazardous areas and to gauge the requirement
of measurement instruments based on size of the system.
iii) As-built verification of drawings for the main steam distribution piping network and study
of the steam distribution system.
iv) Regular interaction with Refinery O&M staff during multiple site visits
b) Evaluating the performance of steam generators:
i) Boiler efficiency was evaluated by indirect method (loss calculation method).
ii) SF Ratio was worked out for Boilers
iii) HRSG efficiency was evaluated by direct method
iv) Efficiency compared with design values
c) Overall Steam balance for the refinery with detailed unit-wise steam Generation & consumption for HP, MP and LP. This also included condensate recovery.
d) Equipment Steam Consumption (Actual) (Measured at site) was compared w.r.t. Equipment Steam Requirement (Design)
Steam Distribution System:
a) Length of main steam distribution header in the entire refinery was ~ 19 km
b) Lines in the refinery were surveyed for areas which get submerged during monsoon as this leads to insulation degradation and heat loss. Accordingly, appropriate suggestions were made.
Steam Leaks and Steam Traps study:
a) Location of steam leaks, nature and quantity of steam lost were summarized Unit wise
b) Steam Losses were quantified by Plume Length Measurement during dry as well as rainy seasons
c) Total Steam Loss due to Steam Leak in the Refinery ~ 100 TPD
d) Approximately 7000 total Steam traps were categorized as OK, Malfunctioning, Failed, Out-of-Service and Missing.
e) Recommended steam trap testing intervals were indicated
f) Recommendations to reduce steam leak were provided.
Condensate Collection:
Additional condensate recovery and utilisation opportunities were identified to the extent of ~5% of steam generated in the refinery.
Steam system Thermal insulation study:
a) Thermal Insulation Survey of Main distribution Header (HP, MP, LP) & Main header inside the Process Units of entire refinery
b) Heat loss measurement was done during dry as well as rainy season
c) Sample observation of Thermal Insulation survey is indicated in Figure-1 & 2 below.
![]() |
![]() |
Figure 1: Visual appearance Photo | Figure 2: Thermal Image |
d) Steam System related items with damaged/poor insulation as well as bare surface were identified.
e) Area required to be thermally insulated was quantified for bare and poorly insulated pipe, Pumps, Valves, bends, flanges.
f) Total Steam Loss (~60 TPD) due to poor Insulation was quantified
g) Cost of steam loss was quantified
h) Suggestions to improve Insulation were made
i) Payback Analysis was done
j) Vendor of Insulating Material were indicated
As the system was large, the data collected was continuously being processed and presented as a draft report mainly for Steam Leak, Boiler performance, Insulation and Steam Traps.
Areas were identified for correction/replacement of faulty steam flow meters and for providing additional steam meters.
TCE already has a wealth of knowledge and experience in conceptualizing and designing steam systems both in domestic and in international arena for varying system sizes and industries to review the Audit findings. Apart from Steam Systems of Thermal Power Plants, TCE has been involved with Steam systems of few refineries.
TCE also has a portfolio of utilisation of Waste Heat/Low Grade Heat/Solar Heat/Surplus Heat.
TCE has been conducting audits for various Plants and buildings since 1985 even before it was mandated by statute. The segments include oil refinery, telecom, buildings, Pulp & Paper plants, Exhibition complex, Tyre, Power Plant, Synthetic fibre, Petroleum Coke; Automotive components related Foundry, Match factory, Water network for Towns and City Municipal Corporations.